Что можно сделать с помощью 3D-принтера для продажи в автомобильном бизнесе
Обновлено: 11.07.2025
В этой статье рассказывается, почему 3D-печать оказала такое большое влияние на автомобильную промышленность и как ее можно внедрить для повышения производительности при одновременном сокращении сроков и затрат.
Автор Билл Артли
Введение
Недавние достижения в области аддитивного производства (или 3D-печати) в автомобильной промышленности открыли двери для новых, более надежных конструкций; более легкие, прочные и безопасные продукты; сокращение сроков выполнения; и снижение затрат. В 2015 году в годовом отчете Wohlers говорилось, что на автомобильную промышленность приходилось 16,1% всех расходов AM. Хотя производители оригинального автомобильного оборудования (OEM) и поставщики в основном используют AM для быстрого прототипирования, техническая траектория AM дает веские основания для его использования в разработке инновационных продуктов и непосредственном производстве в будущем.
В этой статье представлен обзор аддитивного производства в автомобильной промышленности. В нем будут обсуждаться требования к конструкции деталей, используемых в транспортных средствах, а также представлены рекомендации по конструкции для обычных автомобильных приложений. Представлен ряд популярных аддитивных материалов, подходящих для автомобильной промышленности, а также несколько тематических исследований, в которых аддитивное производство было успешно реализовано.
Ручки на руль, напечатанные на 3D-принтере (XT-CF20, FDM) для студенческой гоночной команды Delft
AM в автомобильной промышленности
Общение | Проекты в автомобильной промышленности часто начинаются с масштабных моделей, демонстрирующих форму автомобиля. Они часто также регулярно используются для аэродинамических испытаний. SLA и струйная обработка материалов используются для создания высокодетализированных, гладких масштабных моделей автомобильных конструкций. Точные модели позволяют четко передать замысел проекта и продемонстрировать общую форму концепции. |
Валидация | Прототипирование с использованием AM в настоящее время является обычным явлением в автомобильной промышленности. . От полноразмерного бокового зеркала, напечатанного быстро с помощью недорогого FDM, до высокодетализированной полноцветной приборной панели — существует технология AM, подходящая для любых потребностей в прототипировании. Некоторые инженерные материалы AM также позволяют проводить полное тестирование и проверку производительности прототипа. |
Подготовка к производству | Одна из областей, в которой AM была наиболее разрушительной, — это производство недорогой быстрой оснастки для литья под давлением, термоформования, приспособлений и приспособлений. В автомобильной промышленности это позволяет быстро изготавливать оснастку с низкими затратами, а затем использовать ее для производства мелких и средних партий деталей. Эта проверка снижает риск при инвестировании в дорогостоящее оборудование на этапе производства. |
Производство | Поскольку объемы производства в автомобильной промышленности, как правило, очень высоки ( более 100 000 деталей в год) AM преимущественно использовался в качестве решения для прототипирования, а не для изготовления конечных деталей. Улучшения в размерах промышленных принтеров, скорости, с которой они могут печатать, и доступных материалах означают, что AM теперь является жизнеспособным вариантом для многих производственных циклов среднего размера, особенно для производителей автомобилей более высокого класса, которые ограничивают объемы производства до намного меньше, чем в среднем. |
Индивидуализация | AM оказала значительное влияние на конкурентоспособную автомобильную промышленность, когда стоимость очень сложных одноразовых компонентов оправдано существенным улучшением характеристик автомобиля. Детали могут быть адаптированы к конкретному транспортному средству (индивидуальные легкие рычаги подвески) или водителю (шлем или сиденье). AM также позволил консолидировать детали и оптимизировать топографию многих нестандартных автомобильных компонентов. Это дополнительно подчеркивается в тематических исследованиях, которые можно найти в конце этой статьи. |
Требования к производству автомобилей
Вес – заключительные части
Одним из наиболее важных аспектов, связанных с автомобильной промышленностью, является снижение веса компонентов. В автомобильных приложениях используются передовые инженерные материалы и сложные геометрические формы, чтобы уменьшить вес и улучшить производительность. AM может производить детали из многих легких полимеров и металлов, широко используемых в автомобильной промышленности.
Сложные геометрические фигуры — прототипы и финальные части
На вес и аэродинамику (и, следовательно, на характеристики автомобиля) влияет геометрия детали. В автомобильных деталях часто требуются внутренние каналы для конформного охлаждения, скрытых элементов, тонких стенок, мелких сеток и сложных криволинейных поверхностей.AM позволяет изготавливать очень сложные конструкции, которые при этом могут быть чрезвычайно легкими и стабильными. Он обеспечивает высокую степень свободы проектирования, оптимизацию и интеграцию функциональных возможностей, производство небольших партий по разумной цене на единицу продукции и высокую степень индивидуальной настройки продукта даже при серийном производстве.
Температура — тестирование и заключительные части
Влажность — тестирование и финальные части
Большинство компонентов, которые используются при производстве автомобилей, должны быть влагостойкими, если не полностью влагонепроницаемыми. Одним из основных преимуществ аддитивного производства является то, что все печатные детали могут быть подвергнуты последующей обработке для создания водонепроницаемого и влагостойкого барьера. Кроме того, многие материалы по самой своей природе пригодны для эксплуатации в условиях повышенной влажности и повышенной влажности.
Консолидация деталей — прототипирование и окончательные детали
Количество элементов в сборке можно уменьшить, перепроектировав ее как один сложный компонент. Консолидация деталей является важным фактором при рассмотрении того, как аддитивное производство может помочь сократить использование материалов, тем самым снизив вес и, в конечном счете, стоимость. Объединение деталей также сокращает запасы и означает, что узлы могут быть заменены одной деталью, если потребуется ремонт или техническое обслуживание; еще одно важное соображение для автомобильной промышленности.
Прототипы автомобильных компонентов, созданные с использованием технологий AM
Материалы AM, подходящие для автомобильной промышленности
В таблице ниже представлен ряд материалов, которые используются в автомобильной промышленности, а также их применение.
Приложение | Процесс | Материал | Функции | Пример части |
---|---|---|---|---|
Под капотом | SLS | Нейлон | Термостойкие функциональные части | Крышка аккумуляторного отсека |
Внутренние аксессуары | SLA | Смола | Индивидуальные косметические компоненты | Прототип консоли |
Воздуховоды | SLS | Нейлон | Гибкие воздуховоды и сильфоны | Воздуховоды для кондиционирования воздуха |
Полная шкала панели | Industrial SLA | Смола | Большие детали с обработкой поверхности, сравнимой с литьем под давлением, что позволяет шлифовать и красить | Передний бампер |
Кронштейны и ручки из литого металла | SLA и литые | Воск | Металлические детали, напечатанные на 3D-принтере выкройки | Кронштейн крепления генератора |
Сложный металлический компонент s | DMLS | Металл | Консолидированные, легкие, функциональные металлические детали | Рычажный рычаг подвески |
Рамки | Нанесение струйной печати | Фотополимер | Индивидуальные лицевые панели экрана | Интерфейс приборной панели |
Фары | SLA | Смола | Полностью прозрачные модели с высокой детализацией | Прототипы фар |
Общие автомобильные приложения
Сильфоны
AM (особенно SLS) можно использовать для изготовления полуфункциональных сильфонов, где требуется определенная гибкость при сборке или сопряжении. Как правило, этот материал / процесс лучше всего рассматривать для приложений, где деталь будет подвергаться очень небольшому количеству повторяющихся движений изгиба. Для проектов, требующих значительной гибкости, лучше подходят другие материалы SLS на основе полиэтилена, такие как Duraform «Flex».
Сложные воздуховоды
Используя SLS для производства неструктурных воздуховодов малого объема, таких как воздуховоды системы экологического контроля (ECS) для аэрокосмической отрасли и спортивных гонок, вы можете проектировать высокооптимизированные, очень сложные моноблочные конструкции. С SLS можно проектировать стенки переменной толщины и увеличивать соотношение прочности к весу за счет применения структурно оптимизированных поверхностных лямок. Это очень дорогостоящая деталь для применения с традиционными технологиями производства. Для SLS нет платы за сложность, детали печатаются без поддержки и с высоким уровнем точности.
Сложная функциональная конструкция воздуховода, напечатанная из нейлона SLS
Визуальные прототипы высокой детализации
В отличие от традиционных методов прототипирования, некоторые процессы аддитивного производства позволяют создавать многоцветные конструкции с качеством поверхности, сравнимым с литьем под давлением. Эти модели позволяют конструкторам лучше понять форму и посадку детали. Этот высокоточный метод прототипирования также идеально подходит для аэродинамических испытаний и анализа, поскольку достигаемая отделка поверхности часто является репрезентативной для конечной детали.AM регулярно используется для производства автомобильных компонентов, в которых эстетика важнее функциональности, в результате чего производится все, от боковых зеркал и корпусов фонарей до рулевых колес и полных дизайнов внутренней приборной панели. Распыление материала и SLA-печать — два наиболее распространенных метода, используемых для создания эстетичных прототипов деталей из фотоактивируемой смолы.
Полноцветные текстурированные визуальные прототипы, такие как эта центральная консоль, могут быть созданы с помощью AM
Функциональные монтажные кронштейны
Возможность быстро изготовить сложный и легкий брекет в одночасье – отличительная черта индустрии аддитивного производства. AM не только позволяет изготавливать органические формы и конструкции, но и требует очень небольшого участия оператора, а это означает, что инженеры могут быстро перенести проект с компьютера на сборку за очень короткий промежуток времени. Это невозможно при использовании традиционных производственных технологий, таких как обработка с ЧПУ, где для производства деталей требуется высококвалифицированный оператор станка. Технологии сплавления в порошковом слое, такие как нейлон SLS и печать металлом, лучше всего подходят для функциональных деталей и предлагают широкий спектр материалов (от нейлона PA12 до титана).
Функциональный кронштейн генератора переменного тока, напечатанный с использованием нейлона SLS
Пример 1 — Formula Student в Германии
Formula Student – это международный студенческий конкурс дизайнеров, который был инициирован в США в 1981 году Обществом автомобильных инженеров (SAE) и проводится в Европе с 1998 года. Международные соревнования проходят на гоночных трассах Европы. , США и Азии, и каждая команда самостоятельно решает, в каких соревнованиях она хотела бы принять участие.
В рамках оптимизации своего автомобиля команда Formula Student Germany задалась целью в кратчайшие сроки спроектировать и построить надежную, легкую шарнирно-сочлененную ось (поворотный кулак) с высокой жесткостью. Поворотный кулак должен был выдерживать динамические нагрузки, которым подвергаются гоночные автомобили, а также снижать общий вес автомобиля. В результате конструкция представляла собой топографически сложный отдельный компонент, который можно было изготовить только с использованием технологий аддитивного производства. Для этого случая лучше всего подошла DLMS, поскольку она позволяла изготовить функциональную металлическую деталь со сложной геометрией.
Благодаря оптимизации геометрии поворотного кулака окончательная конструкция стала на 35 % легче исходной конструкции, а ее жесткость увеличилась на 20 %. Использование технологии AM также привело к значительному сокращению времени разработки и производства и повышению надежности на трассе (что, в свою очередь, повысило безопасность).
По сравнению с предыдущими алюминиевыми колесными опорами команде удалось снизить вес автомобиля на 1,5 кг, что сделало его самым легким автомобилем из когда-либо созданных командой.
Окончательный оптимизированный дизайн костяшек
Пример 2 – гонки на мотоциклах Moto2
Выигравшая гонку команда Moto2 TransFIORmers использует передовую технологию аддитивного производства (3D-печать металлом) в нетрадиционной системе передней подвески, чтобы получить значительное конкурентное преимущество. Мотоциклы, участвующие в чемпионате мира MotoGP, особенные; широкая публика не может их купить, и их нельзя использовать на дорогах общего пользования. Как прототипы гоночных велосипедов, они созданы специально для того, чтобы превзойти своих соперников и добиться максимальной производительности на трассе.
При разработке новых компонентов конструкции велосипеда Moto2 приоритетом является снижение веса. В частности, ключевым моментом является снижение «неподрессоренной массы» мотоцикла. Чем меньше неподрессоренная масса, тем лучше подвеска с точки зрения управления вибрацией (дребезжанием) и отзывчивостью как на торможение, так и на ускорение. Французская команда Moto2 TransFIORmers из Перигё, юго-запад Франции, разработала новую конструкцию передней подвески.
Скорость, с которой может быть изменена конструкция нового компонента, и время, необходимое для восстановления, являются важными факторами в конкурентном мире автоспорта. Быстрые и точные итерации деталей имеют решающее значение. Снижение веса, достигнутое металлической 3D-печатью в компоненте поперечного рычага, позволило обойти традиционное явление переноса веса и проблемы, связанные с проблемами тормозного привода. Более того, он позволяет спроектировать деталь, которая не только легче, но и в то же время гораздо более жесткая. Используя подход аддитивного производства к конструкции велосипеда Moto2, TransFIORmers удалось снизить вес своего критического компонента передней подвески на поперечных рычагах на 40%.По сравнению с цельным титановым компонентом и оригинальным сварным стальным компонентом удалось добиться снижения веса на 600 г.
Окончательный оптимизированный дизайн костяшек
Дополнительные ресурсы для инженеров
Производство медицинских устройств: лучшие практики, области применения и правила
Узнайте о процессах, используемых для производства медицинских устройств, и областях их применения, а также о передовых методах проектирования медицинских устройств.
Приложения для аэрокосмической 3D-печати
В этой статье обсуждается, как 3D-печать в настоящее время используется в аэрокосмической промышленности для производства и прототипирования.
Приложения для 3D-печати ювелирных изделий
В этой статье рассказывается, как 3D-печать используется для производства высокодетализированных ювелирных изделий на заказ с помощью литья по выплавляемым моделям и прямой печати металлом.
Приложения для автомобильной 3D-печати
В этой статье рассказывается, почему 3D-печать оказала такое большое влияние на автомобильную промышленность и как ее можно внедрить для повышения производительности при одновременном сокращении сроков и затрат.
Медицинские приложения для 3D-печати
В этой статье обсуждаются требования медицинской отрасли, которые делают AM идеально подходящей технологией для многих приложений.
3D-печать мелкосерийных форм для литья под давлением
В этой статье обсуждается использование 3D-печати для печати форм для мелкосерийного литья под давлением. Включены конструктивные соображения, материалы, конфигурации пресс-форм и сравнительный пример.
Производство медицинских устройств: лучшие практики, области применения и правила
Узнайте о процессах, используемых для производства медицинских устройств, и областях их применения, а также о передовых методах проектирования медицинских устройств.
Приложения для аэрокосмической 3D-печати
В этой статье обсуждается, как 3D-печать в настоящее время используется в аэрокосмической промышленности для производства и прототипирования.
<Р>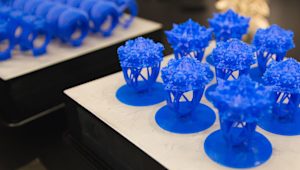
Приложения для 3D-печати ювелирных изделий
В этой статье рассказывается, как 3D-печать используется для производства высокодетализированных ювелирных изделий на заказ с помощью литья по выплавляемым моделям и прямой печати металлом.
Приложения для автомобильной 3D-печати
В этой статье рассказывается, почему 3D-печать оказала такое большое влияние на автомобильную промышленность и как ее можно внедрить для повышения производительности при одновременном сокращении сроков и затрат.
<Р>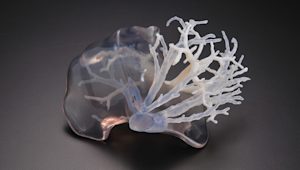
Медицинские приложения для 3D-печати
В этой статье обсуждаются требования медицинской отрасли, которые делают AM идеально подходящей технологией для многих приложений.
<Р>
3D-печать мелкосерийных форм для литья под давлением
В этой статье обсуждается использование 3D-печати для печати форм для мелкосерийного литья под давлением. Включены конструктивные соображения, материалы, конфигурации пресс-форм и сравнительный пример.
Хотя в ближайшее время вы не сможете купить напечатанный на 3D-принтере автомобиль в дилерском центре, 3D-печать уже много лет является важной частью процесса разработки автомобилей. Однако в последнее время мы начинаем видеть, как 3D-печать становится все более популярной в производстве.
3D-печать может значительно повысить ценность цепочек поставок, открывая широкий спектр производственных приложений. Технология становится все более работоспособной и доступной, поскольку компании могут внедрить аддитивное производство собственными силами для поддержки процессов на заводе. Новые эластичные материалы открывают возможности для создания высокоточных функциональных 3D-печатей, которые могут заменить готовые детали и предлагают возможности настройки и высокую производительность, но это только начало.
Читайте дальше, чтобы узнать о пяти основных способах, которыми 3D-печать способствует инновациям в автомобильной промышленности, от проектирования до производства и не только.
Четыре способа, которыми 3D-печать меняет автомобильную промышленность
На этом вебинаре мы обсудим четыре основных способа, которыми 3D-печать способствует инновациям в автомобильной промышленности, от проектирования до производства и не только.
1. Изменение процесса прототипирования
Издавна прототипирование было наиболее распространенным вариантом использования 3D-печати в автомобильной промышленности. Благодаря значительно возросшей скорости создания прототипов с помощью 3D-печати быстрое прототипирование стало практически синонимом 3D-печати, а эта технология произвела революцию в процессе разработки продуктов.
С помощью 3D-печати автомобильные дизайнеры могут быстро изготовить прототип физической детали или узла, от простого элемента интерьера до приборной панели или даже масштабной модели всего автомобиля. Быстрое прототипирование позволяет компаниям превращать идеи в убедительные доказательства концепции. Затем эти концепции могут быть усовершенствованы до высокоточных прототипов, которые точно соответствуют конечному результату и, в конечном итоге, направляют продукты через серию этапов проверки на пути к массовому производству. В автомобильной промышленности такая быстрая проверка абсолютно необходима. "Приостановка производства автомобилей даже на час может обойтись очень дорого, – – сказал Эндрю Эдман, менеджер Formlabs по дизайну, проектированию и производству.
Используя внутреннюю стереолитографию (SLA) для 3D-печати, дизайнеры и инженеры Ringbrothers могут свободно, эффективно и по доступной цене выполнять итерации.
Раньше создание прототипа занимало много времени и, следовательно, было потенциально дорогостоящим, поскольку продукт проходит через большее количество итераций. Благодаря 3D-печати очень убедительные и репрезентативные прототипы могут быть созданы в течение дня при гораздо меньших затратах. Настольные 3D-принтеры позволяют группам инженеров и дизайнеров внедрять технологии внутри компании, чтобы увеличить циклы итераций и сократить расстояние между идеей и конечным продуктом, улучшив общие рабочие процессы разработки продукта.
2. Создание нестандартных, сложных и высокопроизводительных деталей
3D-печать идеально подходит для производства нестандартных деталей с минимальными затратами, предоставляя производителям огромные новые возможности в том, что они могут производить и предлагать своим клиентам.
Небольшим компаниям, которые делают акцент на индивидуальном подходе, например автосалону Ringbrothers, 3D-печать автозапчастей позволяет повысить качество и творческий подход к работе, предоставляя жизненно важные возможности для экспериментов и совершенствования индивидуальных дизайнов. , не беспокоясь о потенциальных затратах и трудоемких производственных процессах, которые в противном случае связаны с настройкой.
Компания Ringbrothers использует 3D-печать для создания нестандартных деталей для конечного использования, таких как этот вентиляционный клапан.
Более крупные компании также сочетают технологию 3D-печати с традиционными средствами. Volkswagen воссоздал свой культовый Microbus 1962 года, заменив его газовый двигатель на 120-сильный электрический привод с крутящим моментом 173 фунт-фут. Концепт «Тип 20» также содержит множество улучшений, обеспечиваемых деталями, напечатанными на 3D-принтере, включая генеративно разработанные литые алюминиевые колеса. Даже колпаки напечатаны на 3D-принтере: хотя они выглядят как штампованная сталь, на самом деле они были изготовлены на 3D-принтере Formlabs SLA, а затем покрыты гальваническим покрытием, чтобы они выглядели и ощущались как металлические детали.
Колпаки этого VW Microbus были напечатаны на 3D-принтере с использованием процесса 3D-печати SLA, а затем покрыты гальваническим покрытием и отполированы, чтобы они выглядели как хромированная сталь. (изображения: VW)
Bentley Speed 6 — еще один пример. Производитель роскошных автомобилей использовал передовую технологию 3D-печати металлом для создания более детализированных и сложных деталей (решетка радиатора, боковые вентиляционные отверстия, дверные ручки и выхлопные трубы), чем те, которые доступны в его текущих серийных моделях.
Компания Bentley использовала технологию 3D-печати металлом для создания сложных деталей с точностью до микрометра. (источник: Бентли)
Но приложения для 3D-печати не ограничиваются классикой, концептуальными или выставочными моделями. Программное обеспечение Twikit для настройки позволило британскому автопроизводителю MINI предложить услуги массовой персонализации своих автомобилей с помощью 3D-печати, что дает покупателям полный контроль над дизайном. Клиенты могут настроить внутренние или внешние компоненты своего автомобиля с помощью ряда шрифтов, узоров и изображений, а также просмотреть свой дизайн с помощью 3D-визуализации.Крайне важно, что для жизнеспособности такого проекта на рынке снижение затрат благодаря модульным компонентам, напечатанным на 3D-принтере, сделало эту форму персонализации доступной для широкой публики.
Сотрудничество MINI с Twikit дает покупателям полный контроль над дизайном для настройки внутренних и внешних компонентов своего автомобиля. Компоненты изготавливаются с помощью 3D-печати для снижения затрат. (источник: Твики)
3D-печать в производстве BMW
Посмотрите, как руководитель проекта BMW Кристиан Грёшель описывает процесс компании по разработке и внедрению программы присадок.
3D-печать также позволила создавать детали, которые невозможно было изготовить никакими другими способами. Ключевым примером является восьмипоршневой моноблочный тормозной суппорт Bugatti. Bugatti отдает предпочтение титану для некоторых компонентов из-за высоких эксплуатационных характеристик материала, но обработка металла традиционными методами является дорогостоящей и сложной задачей. Использование 3D-печати не только позволило Bugatti изготовить суппорт в требуемом масштабе, но и еще больше повысило потенциал его производительности, значительно снизив вес компонента и сделав его значительно жестче и прочнее, чем традиционный вариант производства (алюминий).< /p>
Восьмипоршневой моноблочный тормозной суппорт Bugatti – крупнейшая в мире функциональная титановая деталь автомобиля, напечатанная на 3D-принтере. (источник: Бугатти)
3. Производство инструментов и вспомогательных средств
Инженеры используют вспомогательные средства для производства, чтобы сделать процессы производства и сборки проще и надежнее, сократить время цикла и повысить безопасность рабочих. Автомобильные заводы и поставщики деталей используют тысячи нестандартных приспособлений и приспособлений, каждое из которых адаптировано и оптимизировано для конечного использования. В результате появляется множество нестандартных инструментов, что значительно увеличивает стоимость и сложность производственного процесса.
Передача производства этих нестандартных деталей поставщикам услуг по механической обработке, которые изготавливают детали из цельной заготовки из пластика или металла, может привести к задержке производства на недели, а длительное время выполнения заказа также затрудняет адаптацию к изменениям на заводе.
Аддитивное производство может сократить время выполнения заказа до нескольких часов, а также значительно снизить затраты по сравнению с передачей деталей внешним поставщикам. Поскольку сложность не влечет за собой дополнительных затрат, детали также могут быть лучше оптимизированы для их конечного использования. Новые эластичные материалы для 3D-печати также позволили производителям во многих случаях заменить металлические компоненты пластиковыми деталями, напечатанными на 3D-принтере, или создать прототип и протестировать инструменты перед реализацией.
В результате производство производственных вспомогательных средств с помощью 3D-печати становится одним из крупнейших применений этой технологии.
Pankl Racing Systems использует распечатанные на 3D-принтере приспособления для крепления деталей к конвейерной ленте, когда они проходят ряд этапов обработки.
Например, компания Pankl Racing Systems использует станцию 3D-печати с несколькими 3D-принтерами Formlabs SLA для изготовления жизненно важных производственных инструментов. При изготовлении деталей для узлов редукторов каждая деталь, которую производит компания, требует серии нестандартных приспособлений, приспособлений и других инструментов, разработанных специально для этой детали, поскольку они проходят несколько этапов обработки с использованием токарных автоматов. С помощью 3D-печати инженерам Pankl удалось сократить время изготовления зажимных приспособлений на 90 % — с двух-трех недель до менее чем одного дня — и сократить расходы на 80–90 %, что позволило сэкономить 150 000 долларов США.
Проектирование шаблонов & Светильники с 3D-печатью
Загрузите нашу техническую документацию, чтобы узнать, как снизить затраты, сократить время разработки и создать более оптимизированные рабочие процессы с помощью 3D-печатных приспособлений и приспособлений.
4. Решение проблемы с запчастями
Запасные части исторически представляли собой проблему для автомобильной промышленности. Спрос по своей природе является спорадическим и непредсказуемым, что в некоторых случаях делает стоимость производства запасных компонентов спорным финансовым решением. Однако стоимость продуктов более ненадежна, а ремонт затруднен из-за отсутствия легкодоступных запасных частей. Производство запасных частей в расчете на более поздний спрос также требует больших затрат на хранение.
3D-печать имеет хорошие возможности для существенного положительного решения проблемы запасных частей в автомобильной промышленности. «Я думаю, что самые важные факторы [в решении проблемы запасных частей с помощью 3D-печати] — это получение материалов, которые могут соответствовать характеристикам более традиционных материалов, используемых для деталей, и экономической эффективности. Мы приближаемся к этому», — сказал Эдман. «Вопрос не столько в том, «заменит ли 3D-печать производство запчастей?», сколько в том, когда?»
Благодаря использованию САПР проекты всех деталей можно хранить в виде цифровых копий, что избавляет от необходимости хранить запасы. С распространением настольных 3D-принтеров запасная часть потенциально может быть изготовлена в магазине по запросу клиента.Доступность технологии побудит поставщиков открыть новые возможности для обеспечения легкой поставки компонентов и запасных частей, напечатанных на 3D-принтере.
Даже детали, которые больше не существуют, потенциально могут быть переделаны в соответствии с требованиями путем обратного проектирования на основе цифровых сканирований существующих деталей. Старые модели могут обрести новую жизнь. «У людей есть классические автомобили, которым более 50 лет. Когда-нибудь мы сможем поддерживать их более автоматизированным способом с помощью 3D-печати», — сказал Эдман.
Ringbrother воспроизвел эмблему Cadillac для изготовленного на заказ старинного автомобиля, напечатав форму на 3D-принтере и отлив ее в металл.
5. Упрощение производства деталей общего назначения
Поскольку процессы 3D-печати становятся более доступными с точки зрения стоимости оборудования и используемых материалов, мы увидим постепенный переход к производству обычных автомобильных деталей.
3D-принтеры могут повысить эффективность на этапе изготовления общих деталей. «Там, где вы увидите 3D-печать [методы становятся популярными раньше], есть возможности использовать преимущества добавок для складывания компонентов вместе. У вас может быть сборка из шести или семи автомобильных деталей, которые теперь можно объединить в одну печатную деталь. Вы экономите время и затраты на сборку, даже если отдельная деталь может быть дороже», — сказал Эдман. Благодаря объединению деталей процессы 3D-печати также могут помочь снизить вес и повысить эффективность использования топлива.
Разнообразие материалов, предлагаемых с помощью 3D-печати, начинает соответствовать механическим требованиям различных компонентов автомобиля. Когда аддитивные методы достигнут паритета по затратам с традиционными методами (например, формованием, литьем под давлением), с производственной и финансовой точки зрения будет более целесообразно внедрять 3D-печать в общее производство деталей.
+1. 3D-печатные автомобили
Несмотря на то, что полноценный напечатанный на 3D-принтере автомобиль, готовый к выходу на рынок, еще далеко, уже есть несколько интересных проектов и концепт-каров, которые сигнализируют о том, в каком направлении движется отрасль:
Легкий кокон EDAG. Этот концепт-кар, созданный независимым автомобильным разработчиком EDAG, может похвастаться несущей конструкцией, напечатанной на 3D-принтере в виде ветви, вдохновленной природой. Несмотря на то, что в конструкции используется меньше материала, чем в обычном шасси, все требования, предъявляемые к конструктивно важным компонентам, соблюдены. Чтобы шасси было устойчивым к непогоде, панели кузова обтянуты тканью.
Помимо устойчивости к атмосферным воздействиям, чехол Light Cocoon от EDAG обеспечивает абсолютную свободу, когда речь идет о дизайне и индивидуализации. (источник: ЭДАГ)
The Blade: «Первый в мире напечатанный на 3D-принтере суперкар» предназначен для производства из — по стандартам суперкаров — недорогих материалов, таких как трубы из углеродного волокна и алюминиевые стержни, которые сочетаются с генеративно разработанными 3D-печатными металлическими деталями для добиться малого веса и высокой производительности.
The Blade — это «первый в мире суперкар, напечатанный на 3D-принтере». (Источник: Divergent3D)
Strati: первый в мире электромобиль, в производственном процессе которого широко используется 3D-печать. Автомобиль состоит из 50 отдельных частей, что намного меньше, чем примерно 30 000 деталей, составляющих традиционный автомобиль. Его шасси и большинство конструктивных элементов были напечатаны на 3D-принтере менее чем за 24 часа, и компания стремится сократить это время до менее чем 10 часов.
Strati от Local Motors состоит из 50 отдельных деталей, и на его 3D-печать ушло менее 24 часов.
LSEV: Разработанный итальянской компанией XEV, LSEV может стать первым массовым электромобилем, напечатанным на 3D-принтере, когда он выйдет на рынок в 2020 году. Помимо шасси, сидений и лобового стекла, все видимые части LSEV также печатаются на 3D-принтере. Благодаря широкому использованию 3D-печати компании удалось сократить количество компонентов с 2000 до 57, в результате чего получилась легкая конструкция весом всего 450 кг.
LSEV – это первый электромобиль, напечатанный на 3D-принтере для массового рынка, который, как ожидается, появится на рынке в 2020 году.
Хотя эти проекты и многие другие инициативы по 3D-печати автомобилей остаются на стадии разработки, масштабы распространения 3D-печати в различных областях автомобильной промышленности поразительны. В некоторых случаях технология 3D-печати расширяет границы и помогает открыть совершенно новые возможности в дизайне и производстве. В других технология снижает производственные затраты и экономит время.
По мере того, как понимание ценности 3D-печати продолжает распространяться в отрасли, а технология и доступная материальная база становятся все более универсальными, эта растущая тенденция сохранится.
Автомобильная промышленность сталкивается со спросом на всех фронтах: потребностью в новых, более эффективных автомобилях, а также необходимостью оптимизации производства и рационализации цепочек поставок и логистики. Одной из технологий, которая помогает решить эти проблемы, является 3D-печать.
3D-печать все чаще используется во всех областях автомобилестроения. Помимо широкого использования для быстрого прототипирования, эта технология также используется для производства оснастки и, в некоторых случаях, концевых деталей.
Поскольку спектр приложений для автомобильной 3D-печати продолжает расширяться, ниже приведены некоторые из наиболее многообещающих примеров автомобильных компаний, использующих эту технологию для улучшения своего производства.
1. Сиденья Porsche, напечатанные на 3D-принтере
[Изображение предоставлено Porsche]
Porsche недавно представила новую концепцию сидений для спортивных автомобилей, основанную на 3D-печати и решетчатом дизайне.
Новые сиденья оснащены полиуретановыми 3D-печатными секциями центральной части сиденья и подушки спинки, которые можно настроить по трем уровням жесткости: жесткий, средний и мягкий.
Разрабатывая персонализированные сиденья, немецкий автопроизводитель берет пример с автоспорта, где индивидуальная подгонка сидений для водителя является нормой.
Porsche планирует напечатать на 3D-принтере 40 прототипов сидений для использования на европейских гоночных трассах уже в мае 2020 года, а отзывы клиентов будут использованы для разработки окончательных уличных моделей к середине 2021 года.
В будущем Porsche хочет расширить возможности индивидуальной настройки сидений, помимо их жесткости и цвета, путем персонализации сидений в соответствии с конкретными контурами тела клиента. В настоящее время 3D-печать остается единственной технологией, позволяющей обеспечить такой уровень персонализации.
2. 3D-печать автомобильных кронштейнов
[Изображение предоставлено Rolls Royce]
Кронштейны – это небольшие и довольно простые детали, которые было трудно оптимизировать в прошлом, когда инженеры были ограничены традиционными методами производства. Сегодня инженеры могут проектировать оптимизированные брекеты и воплощать их в жизнь с помощью 3D-печати.
Недавно компания Rolls Royce продемонстрировала возможности 3D-печати брекетов. Компания продемонстрировала большую партию автомобильных металлических деталей, оптимизированных для DfAM и напечатанных на 3D-принтере, многие из которых выглядят как кронштейны.
Экономия средств, более быстрое производство и оптимизация конструкции обычно являются основными причинами использования AM для брекетов.
В примере с Rolls Royce команда смогла включить в детали некоторые действительно интересные функции, в том числе напечатанное на 3D-принтере название бренда и QR-код, а также номера для идентификации конкретной, уникальной детали.
Добавление этих функций в процессе производства возможно только при цифровом производстве, поскольку ни один метод вычитания не может конкурировать с точки зрения стоимости и времени производства.
3. Ford печатает на 3D-принтере детали для высокопроизводительного Mustang Shelby GT500
Ford Motor Company – одна из первых компаний, внедривших 3D-печать: около 30 лет назад она приобрела третий 3D-принтер.
Ford, открывший в прошлом году Центр передовых технологий, предпринял шаги по интеграции 3D-печати в свой цикл разработки продукции. Теперь компания хочет использовать эту технологию для производства приложений.
Одним из примеров тому является последний автомобиль Shelby GT500 2020 года. Сообщается, что Shelby GT500 2020 года поступит в продажу в конце этого года и станет самым аэродинамически совершенным Мустангом на сегодняшний день.
Виртуальное тестирование дизайна было ключевой частью процесса проектирования высокопроизводительного автомобиля. С помощью виртуального тестирования было проанализировано более 500 систем охлаждения и аэродинамических 3D-проектов, что позволило команде достичь целевых показателей прижимной силы, торможения и охлаждения.
После того как были определены наиболее перспективные проекты, команда инженеров Ford использовала 3D-печать для создания и тестирования прототипов. Например, команда напечатала и протестировала более 10 дизайнов плетеных передних сплиттеров, которые они смогли одновременно отправить на тестирование.
Рычаг Ford HVAC, напечатанный на 3D-принтере с использованием технологии Carbon DLS [Изображение предоставлено Ford]
В дополнение к использованию прототипов, напечатанных на 3D-принтере, для проверки конструкции и функционального тестирования, новый Shelby GT500 2020 года также будет иметь два структурных компонента тормозов, напечатанных на 3D-принтере.Эти компоненты были созданы с использованием технологии 3D-печати Carbon Digital Light Synthesis (DLS) и материала EPX (эпоксидная смола) 82 и соответствуют всем стандартам и требованиям Ford по производительности.
С этими приложениями видно, что компания Ford закладывает фундамент, позволяющий делать впечатляющие вещи с помощью аддитивного производства.
«Аддитивное производство будет все больше и больше внедряться в повседневную часть того, чем мы занимаемся как бизнес, — недавно объяснил Гарольд Сирс, технический руководитель Ford по технологиям AM, в серии интервью с экспертами AMFG. «Вместо того, чтобы быть исключением из нормы, это будет гораздо более приемлемо, как это делается».
В будущем будет интересно увидеть, как Ford продолжает использовать возможности 3D-печати для дальнейшего совершенствования производства своих автомобилей.
4. Volkswagen Autoeuropa: производственные инструменты, напечатанные на 3D-принтере
Volkswagen Autoeuropa использует 3D-принтеры Ultimaker для создания приспособлений и приспособлений для своей сборочной линии [Изображение предоставлено Ultimaker]
Хотя прототипирование остается основным применением 3D-печати в автомобильной промышленности, использование этой технологии для изготовления инструментов быстро завоевывает популярность.
Ярким примером этого является Volkswagen, который уже несколько лет использует 3D-печать внутри компании.
В 2014 году компания начала тестировать настольные 3D-принтеры Ultimaker для производства инструментального оборудования на заводе Volkswagen Autoeuropa в Португалии. После успеха пилотного проекта Volkswagen почти полностью перевел производство инструментов на 3D-печать.
Использование технологии для этого приложения дает ряд преимуществ.
Производство инструментов собственными силами снижает затраты на производство инструментов для производителя автомобилей на 90 %, а время выполнения заказов сокращается с недель до нескольких дней. Возьмем один пример: по сообщениям, на разработку такого инструмента, как значок задней двери, потребуется 35 дней с использованием традиционного производства и стоимость до 400 евро. С помощью 3D-печати один и тот же инструмент можно изготовить за четыре дня всего за 10 евро.
Говорят, что использование 3D-печати для инструментов позволило Volkswagen сэкономить почти 325 000 евро в 2017 году, при этом улучшив эргономику, производительность и удовлетворенность операторов.
Что касается производственных вспомогательных средств, 3D-печать быстро развивается как альтернатива более устоявшимся способам изготовления инструментов. Через несколько лет мы, вероятно, увидим, как все больше OEM-производителей автомобилей переходят на инструменты, напечатанные на 3D-принтере, чтобы повысить эффективность своего производства и производительность своих инструментов.
5. Напечатанные на 3D-принтере гайки спасут автомобильные колеса от воров
[Изображение предоставлено Ford Motor Co.]
Как помешать ворам украсть автомобильные колеса? Ford отвечает на этот вопрос, разработав в Европе программу 3D-печати нестандартных колесных гаек для автомобилей, более защищенных от кражи.
Обычно в автомобилях используется одна стопорная гайка на колесо, чтобы предотвратить его снятие без специального ключа, прикрепленного к гаечному ключу. Но их можно победить, поэтому Ford печатает на 3D-принтере шаблоны для своих замков, которые не так просто клонировать.
С помощью 3D-принтеров от EOS Ford создает замки по индивидуальному шаблону для каждого клиента. Используя шаблон звуковой волны из простого предложения, можно создать совершенно уникальный шаблон, обеспечивающий дополнительный уровень безопасности, аналогичный распознаванию отпечатков пальцев.
После разработки замок и ключ печатаются на 3D-принтере как единая деталь из нержавеющей стали. После того, как вы разделите их на части, их нужно лишь немного отполировать, чтобы они заработали.
Преимущество этих замков в том, что их практически невозможно клонировать. Из-за неравномерно расположенных ребер внутри гайки и углублений, которые тем шире, чем глубже они входят, воры не могут сделать восковой оттиск этих замков, не сломав воск.
Повышение безопасности колес и расширение возможностей персонализации продукции — еще одно доказательство того, что 3D-печать меняет правила игры в автомобилестроении.
6. Local Motors и XEV: на пути к автомобилям, напечатанным на 3D-принтере?
Нижняя половина Olli, автономного шаттла, напечатанного на 3D-принтере [Изображение предоставлено Local Motors]
Несмотря на то, что до этого еще далеко, ряд компаний стремятся воплотить в реальность полностью напечатанные на 3D-принтере автомобили.Local Motors, базирующаяся в Аризоне, — одна из компаний, стремящихся к возможности 3D-печати целых автомобилей.
Компания произвела фурор в 2014 году, когда на Международной выставке производственных технологий (IMTS) объявила о первом в истории электромобиле, напечатанном на 3D-принтере — Strati. Автомобиль был изготовлен в сотрудничестве с Окриджской национальной лабораторией (ORNL) и Cincinnati, Inc.
Двумя годами позже компания Local Motors представила Olli — напечатанный на 3D-принтере автономный электрический шаттл, предназначенный для местных низкоскоростных перевозок. Шаттл был разработан в первую очередь для использования в городских центрах, деловых и университетских городках и больницах.
Как же компания добилась этого?
Компания Local Motors использовала одни из крупнейших в мире 3D-принтеров — оборудование для крупномасштабного аддитивного производства ORNL (BAAM) и крупномасштабное аддитивное производство Thermwood (LSAM) — для производства большинства компонентов Olli, включая крышу и нижнюю часть кузова автомобиля.
Аналогичным образом Strati был напечатан на крупномасштабном 3D-принтере Cincinnati, Inc., и на его изготовление ушло всего 44 часа. Колеса и колпаки автомобиля были изготовлены методом прямой 3D-печати металлом.
С момента появления Olli компания Local Motors протестировала более 2000 комбинаций печатного материала и укрепляющих добавок и теперь может напечатать весь микроавтобус примерно за 10 часов.
Local Motors связывает свой успех с "цифровой моделью производства автомобилей" . Эта бизнес-модель позволяет компании выводить продукты на рынок совершенно новым способом, создавая новые проекты совместно с мировым сообществом экспертов. Компания использует цифровые производственные технологии, такие как 3D-печать, для производства и сборки автомобилей на местных микрофабриках.
3D-печать естественным образом подходит для этой модели распределенного производства, так как позволяет быстро повторять проекты, настраивать детали и продукты по мере необходимости, экономя ресурсы и уменьшая потребность в хранении запасов.
>Несмотря на то, что потребуется некоторое время, чтобы увидеть на дорогах полностью напечатанные на 3D-принтере автомобили, такие проекты, как Olli от Local Motors, могут приблизить нас на один шаг к этой захватывающей возможности.
Local Motors — не единственная компания, занимающаяся 3D-печатью автомобилей. Точно так же итальянский автопроизводитель XEV разрабатывает низкоскоростной электрический автомобиль LSEV с помощью 3D-печати.
Используя широкоформатную технологию FDM и четыре различных сорта полиамида и ТПУ, компания может сократить свои производственные затраты на 70% и воспользоваться преимуществами облегченных предложений 3D-печати.
Готовый LSEV весит всего 450 кг и состоит всего из 57 пластиковых компонентов, что означает, что его можно изготовить за считанные дни. XEV также приняла решение произвести 2000 собственных широкоформатных экструзионных 3D-принтеров для использования на своих заводах в производстве.
Хотя массовое производство автомобиля начнется в конце этого года, предварительные заказы уже были сделаны итальянской почтовой службой Post Italiane, которая заказала для своих операций 5000 автомобилей, изготовленных по индивидуальному заказу.
Введение в 3D-печать в автомобильной промышленности
По мере того, как 3D-принтеры становятся дешевле, быстрее и точнее в работе, все больше отраслей находят для них применение. Одной из крупных отраслей, которая за последнее десятилетие полюбила 3D-принтеры, является автомобильная промышленность. Некоторые крупнейшие производители автомобилей используют эту технологию, чтобы одержать верх над своими конкурентами.
В этой части мы углубимся в автомобильную промышленность. Мы узнаем, как используются 3D-принтеры, какова их роль, кто их использует и почему эта технология так полезна для них.
Роль 3D-печати в автомобильной промышленности
Роль 3D-печати в автомобильной промышленности больше, чем вы думаете. В последнее десятилетие все больше и больше автомобильных компаний бросают вызов 3D-печати.
Роль 3D-печати не очевидна обычному потребителю, поскольку мы не видим на дорогах машин, напечатанных на 3D-принтере. Настоящая роль проявляется, когда вы отодвигаете занавес и смотрите на процессы производства и тестирования.
Как вы увидите в следующих разделах, 3D-печать — это правильный производственный процесс для каждой автомобильной компании.
Где можно найти напечатанные на 3D-принтере автозапчасти
Не так много 3D-печатных деталей превращаются в окончательный производственный цикл. Это не значит, что напечатанные на 3D-принтере детали — это плохо, просто их сложно напечатать в масштабе, необходимом производителям автомобилей.
В тестовой лаборатории
Большинство напечатанных деталей появляется на этапах прототипирования и тестирования. Например, команда Alfa Romeo F1 печатает на 3D-принтере уменьшенные модели своего окончательного серийного автомобиля. Они отправляют миниатюрные детали в аэродинамическую трубу, чтобы посмотреть, насколько аэродинамической будет машина.
Этот вариант намного дешевле, быстрее и проще, чем изготовление полноразмерной модели с последующим ее тестированием.
То же самое можно сказать о нагрузочных испытаниях, сборочных испытаниях и динамических ситуациях для автомобильных деталей.
Инструменты, приспособления и приспособления
Сотрудники Ford используют 3D-принтеры для изготовления инструментов, приспособлений и приспособлений для своих автомобилей. Они используются как второстепенные этапы конечного производственного процесса.
Для создания автомобиля может потребоваться множество уникальных инструментов. Вместо того, чтобы платить стороннему поставщику по завышенной цене, эти команды решают печатать собственные инструменты.
Замена устаревших деталей для классических автомобилей
Если у вас есть что-то вроде Chevelle 74 года, вы знаете, что заменить сломанную деталь практически невозможно. Настоящие коллекционеры будут устанавливать в свои автомобили только оригинальные запчасти, но у большинства из них возникают проблемы.
Например, Chevelle не видел производственной линии с 1977 года. Владельцам приходится скрестить пальцы в надежде найти замену сломанной оконной ручке.
Кроме того, деталь можно распечатать на 3D-принтере с использованием размеров OEM. Результат? Квази-OEM-деталь, о которой никто не сможет сказать, является реплицированной деталью. В то же время это намного дешевле, чем оригинальная деталь.
Какие автомобильные компании используют 3D-принтеры?
- БМВ
- Ауди
- Порше
- Форд
- Вольво
- Бугатти
- ГМ
- Роллс-Ройс
- Дайхатсу
- Фольксваген
- Команда Alfa Romeo F1
Преимущества 3D-печати для автомобильной промышленности
Если эти громкие имена в автомобильной промышленности используют 3D-печать, для этого должна быть веская причина. Что ж, есть ряд причин, по которым 3D-принтеры так полезны в этой отрасли. Давайте поговорим о некоторых из основных.
Цена
Прежде всего, производство малосерийных или одноразовых деталей невероятно дорого, если вы используете традиционную механическую обработку.
Существуют затраты, связанные с покупкой сырья, настройкой станков, изучением деталей и, наконец, их изготовлением. В традиционных механических мастерских стоимость «за единицу» снижается по мере того, как вы производите все больше и больше. Одноразовые детали имеют максимально возможную стоимость «за единицу».
Для большинства серийных автомобилей они будут использовать массовое производство для производства сотен тысяч деталей. Перед окончательным производственным циклом, на начальных этапах, этим производителям может понадобиться всего 10 или 20 деталей для экспериментов.
Вместо того, чтобы тратить огромные суммы на механический цех, эти компании могут использовать цех 3D-печати. Им понравится гораздо более низкая цена на большинство товаров, которые они рассматривают.
Деталь, стоимость которой составляет 5000 долларов США, может стоить всего 500 долларов США при 3D-печати.
Скорость изготовления
Детали, напечатанные на 3D-принтере, не только дешевле, но и быстрее изготавливаются. Автомобильные детали могут быть очень сложными, поэтому их обработка может потребовать много времени, энергии и талантливого механика.
Вместо того, чтобы долго ждать традиционной механической обработки, автомобильная компания может обратиться в цех 3D-печати. Для особо сложных деталей они могут сэкономить недели или месяцы на этапе подготовки.
Простота итеративного проектирования
На этапе прототипирования происходит множество итераций. Дизайнеры могут пройти через дюжину прототипов, каждый с небольшими изменениями по сравнению с предыдущей версией. Эти настройки происходят после того, как они подержат прототип в руках и физически протестируют его.
Каждая из этих итераций требует больше денег и времени, затрачиваемых на ожидание, пока механик закончит деталь. С помощью 3D-принтера дизайнер может внести изменения и начать печать новой детали в тот же день.
Легко внести изменения в 3D-модель CAD и отправить ее в мастерскую 3D-печати.
Подтверждение концепции
Иногда у автодизайнера есть идея, но он не совсем уверен, как она сработает. Им было бы трудно просить у своего босса тысячи долларов, чтобы проверить идею, которая может даже не сработать.
Им гораздо проще попросить десятки или сотни долларов за 3D-печать одного и того же изделия.
Это один из способов, с помощью которого компания BMW может опережать своих конкурентов благодаря линейке M Performance. Если у кого-то есть идея для новой, легкой и высокопроизводительной дверной панели, он может протестировать ее и проверить, прежде чем перейти к полномасштабному производству.
Облегчение
Проектирование детали для 3D-принтера сильно отличается от ее проектирования для фрезерного станка с ЧПУ. С 3D-принтером у вас больше свободы в дизайне.
Одним из способов свободы является возможность облегчить изделие. Bugatti хотели сделать тормозной суппорт легче, поэтому они напечатали его на 3D-принтере, и он попал в заголовки газет по всему миру.
Можно ли напечатать на 3D-принтере целый автомобиль?
До сих пор мы говорили только о напечатанных на 3D-принтере компонентах или деталях автомобиля. Можно ли распечатать целую машину? Это не только возможно, но это уже делалось несколько раз.
3D-принтеры могут использовать множество различных материалов и печатать почти все, что можно изготовить другим способом. Комбинация углеродного волокна, пластика и металлов позволяет легко представить, как кто-то может напечатать на 3D-принтере целый автомобиль.
Единственное место, где 3D-печать не работает, — это электрические компоненты, шины, двигатель и подвеска. На данный момент, вероятно, проще просто купить и установить эти компоненты в полностью напечатанный на 3D-принтере автомобиль.
Местные моторы Strati
Компания Local Motors напечатала свои Strati на 3D-принтере. Единственными деталями, не напечатанными на 3D-принтере, являются двигатель, аккумулятор, подвеска и фары. Все это можно напечатать менее чем за 24 часа, а цель — сократить время печати до 10 часов.
Ламбо, напечатанный на 3D-принтере
Как насчет чего-то более стильного? Что ж, дуэт отца и сына собрал 3D-печатный Lamborghini Aventador. Это не может быть намного круче, чем это.
Концепт-кар, напечатанный на 3D-принтере
Еще один отличный пример – напечатанный на 3D-принтере Light Cocoon от EDAG. Этот проект начался в 2015 году, и они успешно собрали несколько 3D-печатных концептуальных автомобилей, которые выглядят великолепно.
Преимущество заключается в том, насколько легкий автомобиль. Тонкий слой покрывает решетчатый каркас автомобиля, что возможно только с помощью технологии 3D-печати.
Что делать потребителям, которые хотят печатать на 3D-принтере детали для своих автомобилей?
Единственный недостаток 3D-печати в автомобильной промышленности — это когда дело доходит до потребителей. У вас нет дешевого способа распечатать что-то на 3D-принтере для вашего личного автомобиля. Заказные одноразовые детали имеют большую цену, если проектная работа еще не завершена.
Запчасти для автомобилей должны быть специально разработаны, что требует значительных денежных и временных затрат. Если у вас еще нет проекта, вас может застать врасплох цитата из профессионального магазина 3D-печати.
Возможно, вы захотите использовать модификации вторичного рынка, если хотите настроить свой автомобиль.
Материалы, используемые в автомобильной 3D-печати
Чтобы лучше понять автомобильную 3D-печать, давайте поговорим о некоторых материалах, которые вы можете использовать.
Пластик
Конечно, люди думают о пластике, когда представляют себе 3D-печать. В нашем магазине мы можем изготовить массивные изделия размером до 60″ x 29″ x 22″.
Они не так прочны, как металлы, но дешевле.
Нержавеющая сталь
Высокая прочность, низкая гибкость и коррозионная стойкость. Вот почему так много людей в автомобильной промышленности любят нержавеющую сталь.
Знаете ли вы, что нержавеющую сталь можно распечатать на 3D-принтере? С точки зрения материалов конечный продукт идентичен необработанной нержавеющей стали.
Этот материал мы можем использовать для изготовления форм для отливки изделий.
Стальная сталь
Маркерообрабатывающая сталь обычно используется для инструментов для литья под давлением. Они помогают производителям автомобилей производить пластиковые детали оптом. Как правило, изготовление формы с помощью 3D-печати дешевле и быстрее, чем традиционная механическая обработка.
Голубой камень
Если вам нужна модель аэродинамической трубы, вы можете рассчитывать на Bluestone. Это строительный материал, представляющий собой стабильный инженерный нанокомпозит. Он идеально подходит для прототипирования аэродинамики или создания масштабной модели автомобиля или велосипеда.
Подробнее об автомобильной 3D-печати
Мы очень рады тому, как много автомобильных компаний используют 3D-принтеры. Мы уже давно об этом говорим, но 3D-печать — это прорыв для автомобильной промышленности. Компании могут создавать прототипы, тестировать идеи и производить небольшие партии продукции дешевле, быстрее и точнее, чем в традиционном механическом цехе.
Если вы хотите узнать больше об автомобильной 3D-печати или вам нужна 3D-печать для вашей автомобильной компании, обратитесь к нашим специалистам в отделе 3D-печатных деталей. У нас есть опыт и знания, чтобы помочь с вашим проектом 3D-печати.
Отправить комментарий Отменить ответ
Этот сайт использует Akismet для уменьшения количества спама. Узнайте, как обрабатываются данные ваших комментариев.
Читайте также: